Proven productivity of the BPS-Pastiller process The ideal solution for de-bottlenecking or revamping urea processing facilities – produce high quality pastilles in an economical and environmentally friendly manner. The BPS-Pastiller system can be used to process fertilizer urea, technical urea, Adblue, animal feed, Speciality urea products such as urea and sulphur, USA, U+P, U+K, urea and micronutrients. Multiple units operating in parallel enable capacities of more than 2500tpd. Inside the BPS-Pastiller, urea melt is transformed into regulare droplets which are applied across the entire travel long with the belt, As they travel along with the belt, they cool and solidify before being discharged and conveyed for storage. The circumferential speed of the BPS-Pastiller is synchronized with the speed of the steel belt cooler, ensuring that drops are deposited without deformation to deliver regular pastilles with an optimum shape. Other special fertilizer products suitable for BPS-Pastiller solidification Include: Ammonium nitrate and additives Magnesium nitrate Calcium nitrate NPK products High product quality Excellent size distribution:99,75%between 2-4mm diameter High average crushing strength:56n High shock resistance:0,49% Low abrasion during handling and, as a result, low visible dust generation Low bullet content No formaldehyde required Environmental benefits Indirect heat transfer-no contact between product and cooling media No air cleaning necessary Low missions: dust<5mg/m3,ammonia<50mg/ m3 System efficiency From liquid to solid in a single step Simple process requiring minimal equipment No scrubbing, screening, recycling, crushing or bulk cooling Production versatility High production flexibility with several BPS-Pastiller units operating in parallel Rapid change-over to partial operation-no stop in production or change in quality Quick start-up and shut-down of plant Economical benefits Initial investment costs 30-60%lower than competitive systems Very low energy consumption:4kw/t of urea No use of chemicals such as formaldehyde Low especial foundations required, simple installation on ground floor
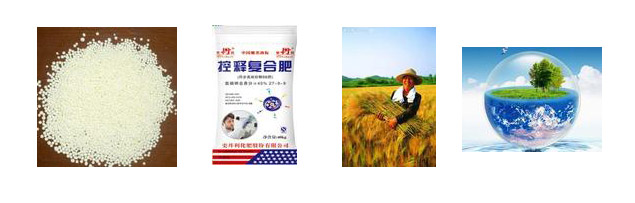 |