Biquick BPS-Pastiller system has remained one of the most popular and efficient pastillation systems on the market, Now completed for a wide variety of applications and products. The BPS-Pastiller process is economical and reliable, delivering dust-free pastilles that provide all the key advantages of this product from, i.e easy product flow and high bulk weight for easy bagging, transportation, storage, metering, blending and re-melting. It provides a product that’s highly uniform, hemispherical, stable, thermally unstressed and of high purity and quality. The BPS-Pastiller can be equipped with different metering systems to produce pastille of precise the right size, from micro pastille up to 30mm.products with melting temperatures up to 300℃are suitable for this process as are those with viscosities from 1 to 50,000mpas. BPS-Pastiller in operation Molten product is fed to the BPS-Pastiller via a pump and then uniformly deposited-in the form of drops-across the full width of the steel belt – max.1.5m. A special design with no reciprocating or oscillating parts means minimal wear, easy maintenance, quick handling and simplified product changeover. Excellent product quality BPS-Pastiller produces premium quality pastilles of a consistent size for a better quality end produce. Efficiency & economy Uniform size means easy dosing and metering for more efficient handling and packing. Environmentally friendlier With no edges or corners to break off, BPS-Pastiller are dust-free for a healthier environment. Cooling Biquick Steel belt cooling systems (single and double belt)are designed for continuous production in the chemical, food an plastics industries Mixing and grinding Preparation A range of different solid derivates can be mixed with the urea melt (in concentrations of between 1-50%)to produce special fertilizer products. The solid derivates are – by means of a precise gravimetric weight – in the urea flow into the inline mixer and grinder. here the solid particles are mixed homogeneously and ground. If necessary, a second fine grinder can be installed to achieve micro grains of less than 180um.this eliminates the possibility of plugging inside the BPS-Pastiller and ensures continuous operation. From here the slurry product is feed to the BPS-Pastiller for pastillation A major benefit of the BPS-Pastiller system is that multiple units can be operated in parallel to achieve the specific capacity required by a producer. This offers significant advantages in terms of flexibility. the BPS-Pastiller units can be connected and controlled in such a way that individual units can be shut down the whole plant. once cleaning or maintenance has been carried out, the unit can be restarted in minutes. A major benefit of the BPS-Pastiller system is that multiple units can be operated in parallel to achieve the specific capacity required by a producer. Process Date
Liquid urea |
Urea concentration to the BPS-Pastiller:
|
|
Inside of BPS-Pastiller:
|
|
Product feeding temperature:
|
|
Product feeding pressure:
|
|
Cooling water temperature:
|
|
Solid urea |
Shape:
|
|
Diameter for 50:
|
|
Angle of repose:
|
|
Pastilles discharge temperature:
|
|
Capacities |
Capacity range per unit:
|
|
Operational availability:
|
|
Consumption |
Electrical :
|
|
Steam:
|
|
Cooling agent:
|
|
Air:
|
|
Formaldehyde additive:
|
| Process control PLC controlled system with automatic flushing, automatic belt tracking and tensioning system, all safety features etc. Dimensions
Main dimensions of one unit |
Length:
|
|
Width:
|
|
Height:
|
|
Cooling length:
|
|
Weight/unit:
|
|
Material of constructi0on for steel base, Frame, drums, steel belt, hood, cover
|
|
Product Quality High-quality Virtually dust-free pastilles High crushing strength, high shock resistance, a uniform pastille size(adjustable from 2-4mm)results in an end product with virtually no dust content, ideal for subsequent handling, storage, transportation and application as a fertilizer. Premium quality Product The BPS-Pastiller process delivers a premium quality product offering the following qualities: Pastilles of a large and uniform size Excellent size distribution High average crushing strength High shock resistance Low abrasion during handling Low bullet increase No formaldehyde required Free-flowing product Excellent field distribution System Efficiency From liquid to solid in a single step Simple process requiring minimal equipment No scrubbing, screening, recycling, crushing or bulk cooling. Well-defined cooling time for complete and efficient shock crystallization Production versatile (Highly versatile Process) The fact that several BPS-Pastiller solidification lines can be run in parallel offers a high degree of versatility and the ability to handle anything from 100 to more than 2500 tpd. it is also easy to change over to partial operation without stopping production or affecting product quality. Significantly Lower costs Initial investment costs an be anything up to 60% lower than those of competitive systems, while energy costs are substantially lower too. the inherent simplicity of the system also means fewer spare parts and easy cleaning. Intial investment costs 30-60% lower than competite systems. High availability of the plant: 8500-8700h/year. Individual BPS-Pastillerers can be stopped for cleaning or maintenance without shutting down the entire pant (unlike competitice systems), increasing efficiency and lowering operational costs. Very low energy use: electrical consult motion just 4 kw/t of urea. No need for chemicals such as formaldehyde for forming. No air scrubbing necessary; no chemicals required for neutralization. Very simple process(BPS-Pastillerer uses just two motors)means maintain cost are very low. Low erection costs due to: Delivery as skid mounted equipment No special foundations required Simple installation on ground floor Services Our expertise in plant design enables us to engineer and supply customized solutions for fertilizer production, covering everything from liquid product supply and the solidification process right through to downstream transportation, storage and bagging. Our engineering know-how means we can provide a complete service covering erection, start up and training. Modular systems The front end of our systems usually incorporates a feeding device which delivers the product onto the belt. The heart of our systems is always a steel belt which is arranged as a double belt or a single belt. At the end of most systems is a discharge device which removes the processed product from the belt. Biquick process systems is a single source supplier of processing plants, steel belts and associated service support, providing complete installations for customers across the petrochemical, chemical, plastics and food industries. Among the chemical products for which we supply granulation systems are: Sulphur Fertilizer Waxes Resins Fine chemicals We have extensive experience in these markets, and our record of partnership, innovation and system development is unparalleled. this in-depth understanding of customer needs puts us in a unique position to be able to offer: Feasibility studies Test and pilot production Engineering/project management Manufacturing, supply& installation Start-up ,spares/service How large or small your requirements are, we can provide complete system installations ready for full production, and we can support these through our worldwide service network.
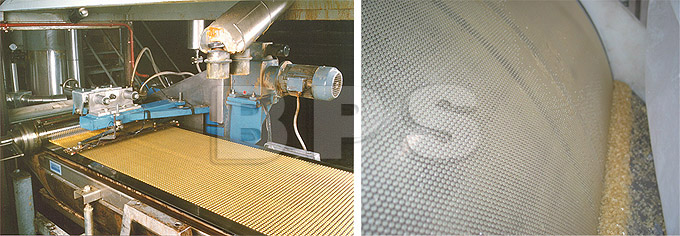
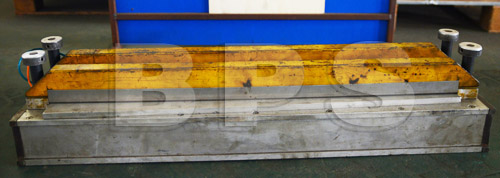 |